Lesedauer: 4 Minuten
Gastbeitrag: Hochschule Schmalkalden und Technische Universität Ilmenau
Smarte Aluminium-Spritzgießwerkzeuge
Industrielle Produktion ist ohne spritzgegossene Produkte aus Kunststoffen wirtschaftlich, qualitativ und ökologisch nahezu unmöglich. Eine schiere Vielzahl von Produkten in unserem alltäglichen Umfeld entstammen dem Spritzgießprozess.
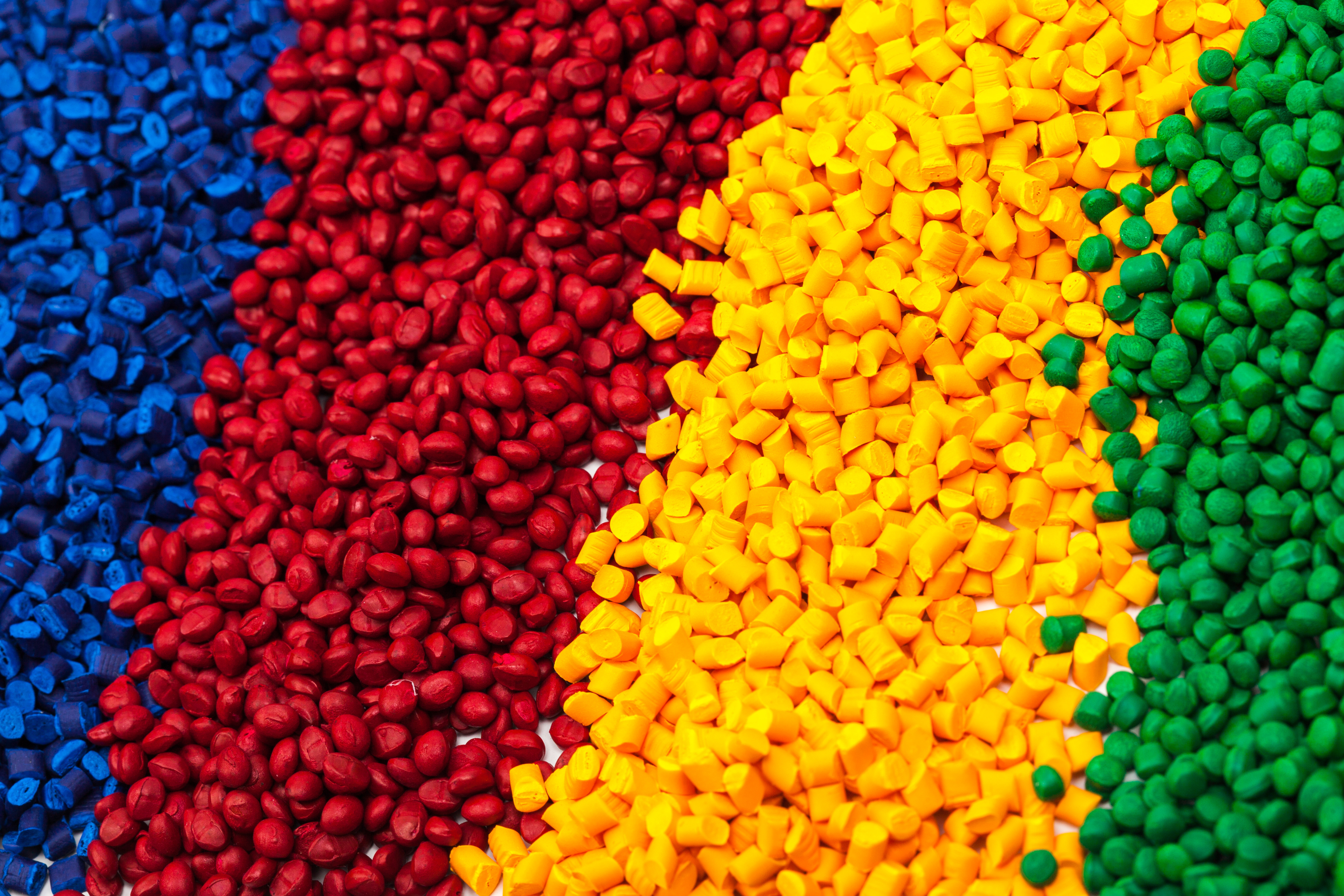
© AdobeStock
Ohne die Kunststofftechnik könnten beispielsweise viele Konstruktionen gar nicht umgesetzt oder heutige Forderungen nach Energie- und Materialeffizienz nicht erfüllt werden. Umso wichtiger ist es, diesen elementaren Wirtschaftszweig effizienter und damit nachhaltiger zu gestalten.
Spritzgießwerkzeuge aus Aluminium oder Stahl
Für die Serienproduktion werden Spritzgießwerkzeuge überwiegend aus Stahlwerkstoffen hergestellt, da diese eine vermeintlich höhere Standzeit im Vergleich zu Aluminiumlegierungen aufweisen, die gegenwärtig nur für Prototypen Verwendung finden. Dabei besitzt Aluminium gegenüber Stahl eine deutlich bessere Wärmeleitfähigkeit, wodurch der Produktionsprozess erheblich verkürzt werden kann. Die Kunststoffschmelze kühlt in einer Form aus Aluminium schneller kontrolliert ab und das Bauteil kann früher entformt werden. Das spart nicht nur Zeit, sondern auch Energie und Kosten. Für nachhaltigere Produktionsprozesse sowohl im Werkzeugbau als auch im Spritzgießen ist also Aluminium als Werkstoff zu bevorzugen.
Das Projekt AlPro (Smarte Aluminium Spritzgießwerkzeuge mittels WAAM und KI Methoden für energieeffiziente und ressourcenschonende Produktionsprozess) zielt darauf ab, Spritzgießwerkzeuge mittels 3D-Druck aus Aluminiumlegierungen herzustellen. Im Ergebnis sollen die Werkzeuge energieeffizient, ressourcenschonend und qualifiziert für eine Serienproduktion sein.
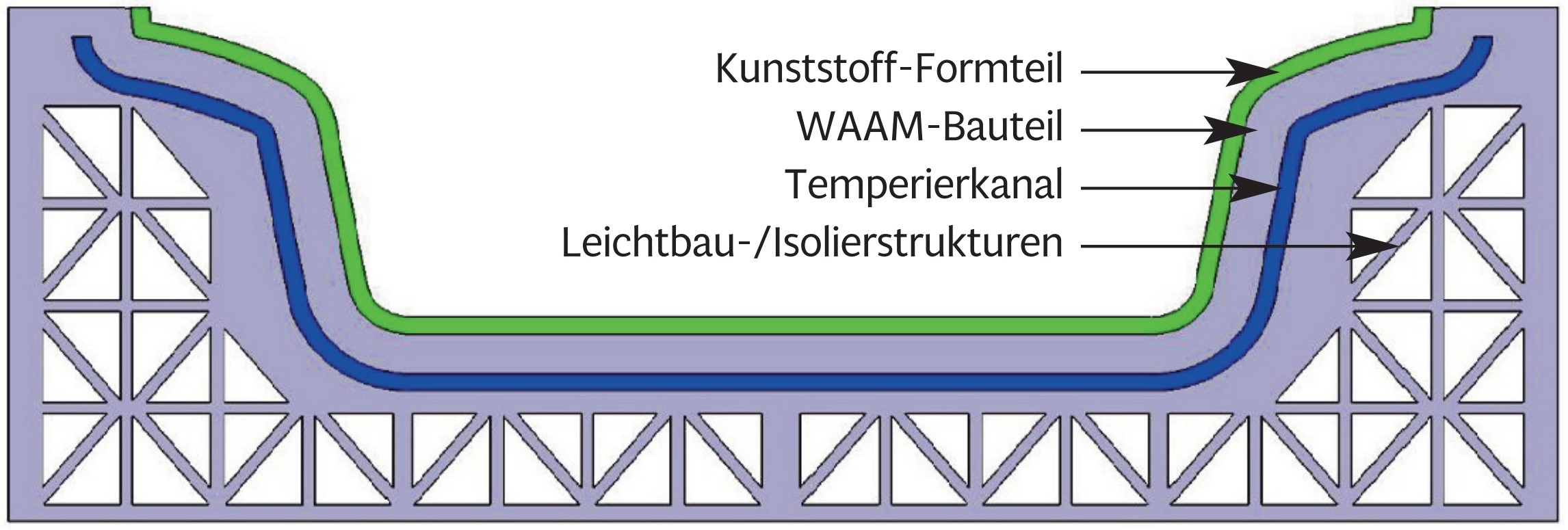
Additiv gefertigtes Bauteil im Querschnitt (Foto: HS Schmalkalden)
Additives und subtraktives Spritzgussverfahren
Als additives Verfahren findet ein lichtbogenbasiertes Auftrag schweißen (Directed Energy Deposition-Arc (DED-Arc)) mit einer hohen Auftragrate bis 5 kg pro Stunde Anwendung. Damit können großvolumige Bauteile wie Spritzgießwerkzeuge in einem vertretbaren Zeitraum gefertigt werden. Der Vorteil im Vergleich zu einem subtraktiven oder spanenden Verfahren ist die Generierung von konturnahen Temperierkanälen, die die Abkühlgeschwindigkeit nochmals er höhen und für eine gleichmäßige Abkühlung des Bauteils sorgen.
Darüber hinaus können unterschiedliche Aluminiumlegierungen stoffschlüssig eingesetzt werden. Der Grundkörper besteht aus einer günstigeren Legierung, während an der Oberfläche und insbesondere am Einspritzbereich verschleißfeste Aluminiumwerkstoffe ihren Einsatz finden. Ein besonderes Augenmerk liegt im Projekt auf dem Verschleiß des Spritzgießwerkzeuges. Der Verschleiß Zustand wird mittels Körperschall Sensorik und Computertomographie permanent überwacht. Härtemessungen und Gefügeuntersuchungen am Werkzeug komplettieren die Kontrolle. Während des Spritzgießprozesses werden die Maschineneinspritzdrücke und Temperaturen im Werkzeug aufgenommen und die gefertigten Bauteile auf Verzug und Oberflächenabweichungen untersucht.
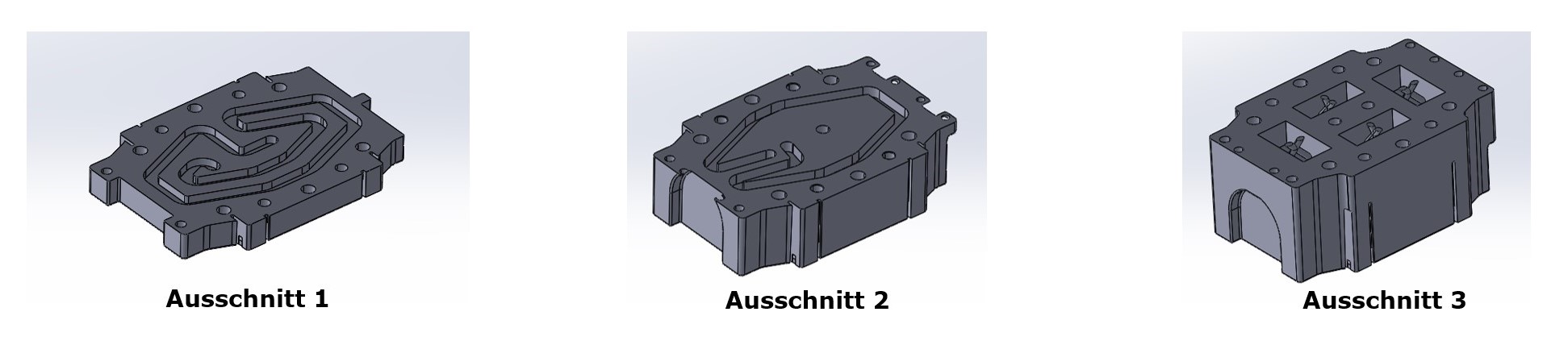
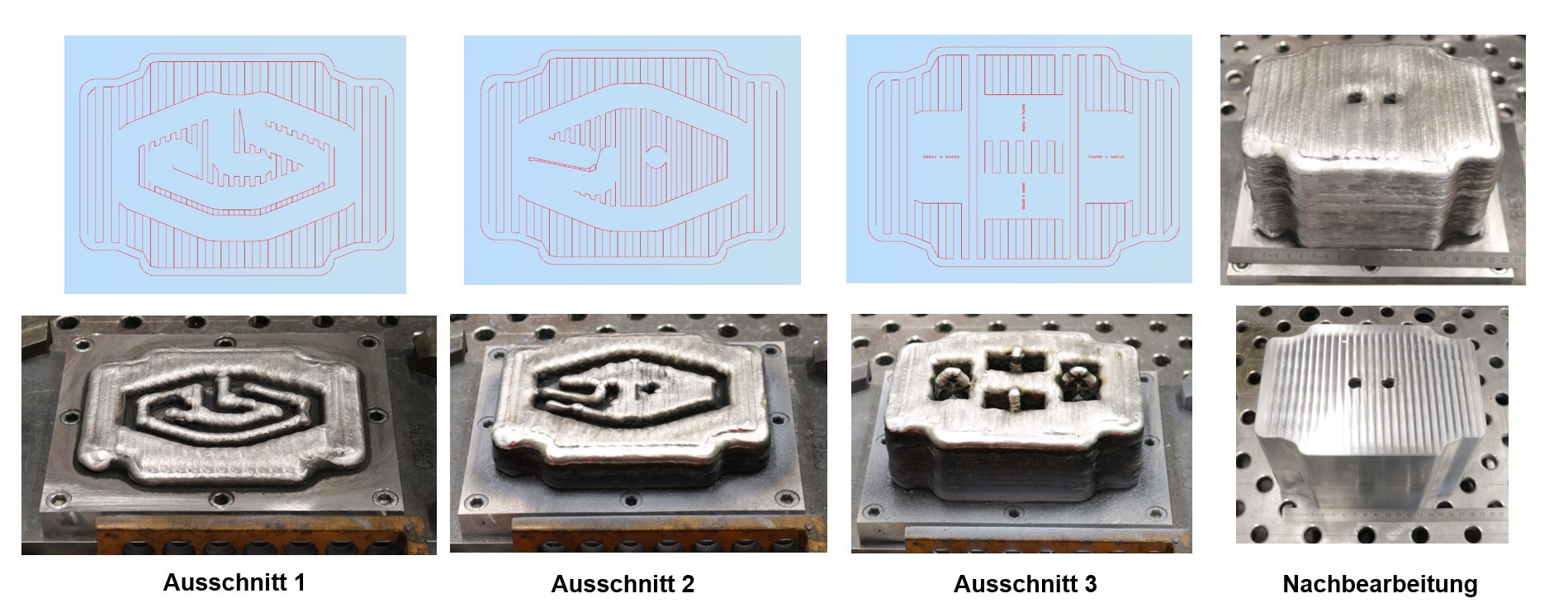
Aufbau eines Werkzeugs mit innen liegenden Temperierkanälen mittels DED-Arc-Prozess aus einem abgeschlossenem Projekt (Foto: HS Schmalkalden)
Nutzung von KI zur Verringerung des Werkzeug-Verschleises
Methoden des Maschinellen Lernens (KI) führen alle gewonnenen Daten aus Prozess und Werkzeug zusammen und prognostizieren die Standzeit des Werkzeugs. Damit können in Zukunft gezielt die passenden Legierungen ausgewählt werden, um den Verschleiß zu reduzieren, die Reproduzierbarkeit des Prozesses zu erhöhen und sowohl die Standzeit der Spritzgießwerkzeuge als auch die Bauteilqualität zu maximieren.
Am Beispiel eines in einem bereits abgeschlossenen Projekt (siehe Abbildung) untersuchten Lebensmittelbehälters aus Kunststoff konnte bereits durch den Einsatz eines optimierten und additiv gefertigten Aluminiumspritzgießwerkzeugs die Zykluszeit um 28 Prozent reduziert, die Einfallstellen auf der Kunststoffoberfläche um 24 Prozent minimiert und die Verfügbarkeit des Werkzeugs um 139 Stunden im Monat gesteigert werden. Bei einer Gewichtsreduktion des Werkzeugs um 65 Prozent gegenüber Stahl konnten auch nach 136.000 Zyklen keine Verschleißerscheinungen festgestellt werden. Darüber hinaus weisen die Bauteile aus dem Aluminiumwerkzeug geringere Eigenspannungen auf. Mit dem Transfer der bisherigen Ergebnisse sind Thüringer Werkzeug und Formenbauer in der Lage, neuartige und nachhaltige Spritzgießwerkzeuge zu fertigen und dabei durch Einsatz der additiven Technologie DED-Arc Energie, Material und Zeit bei der Fertigung einzusparen.
Unternehmen des Werkzeug- und Formenbaus stehen in der Wertschöpfungskette der Kunststofftechnik weit vorne. Dadurch profitieren auch die mit nachgelagerten Produktionsschritten befassten Unternehmen wie Kunststoffverarbeiter durch die sinkenden Kosten im Spritzgießprozess. Zusätzlich können die gewonnenen Erkenntnisse auch auf andere Werkzeuge in der Stanz- und Umformtechnik übertragen werden.
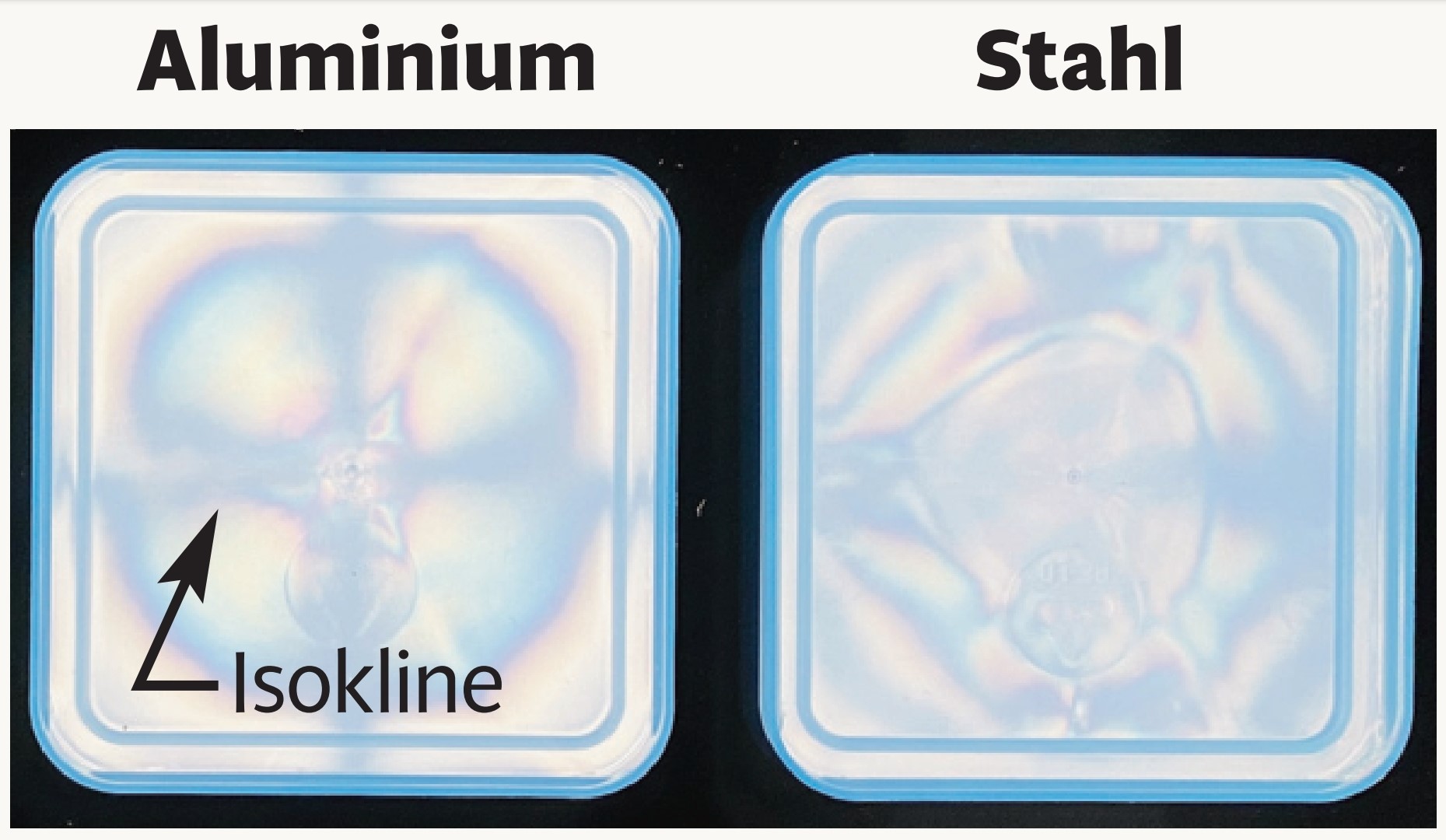
Verringerte Eigenspannung durch homogene Abkühlung im Aluminiumwerkzeug (Foto: HS Schmalkalden)