Lesedauer: 5 Minuten
Gastbeitrag: IMMS Institut für Mikroelektronik- und Mechatronik-Systeme gemeinnützige GmbH
Optimierung der Energieeffizienz und Wartung mittels Sensorik und Künstlicher Intelligenz
Sensorplattform „sUSe“
Einerseits ist Energie derzeit im Vergleich zur Vergangenheit preisintensiv, andererseits ist die Beschaffung von unternehmensrelevanten Komponenten aufgrund der weltweiten Lieferkettenschwierigkeiten problematisch.
Es ist daher wichtig, Energie zu sparen, sie optimal zu nutzen und dem Ausfall von Maschinen und Anlagen vorzubeugen.
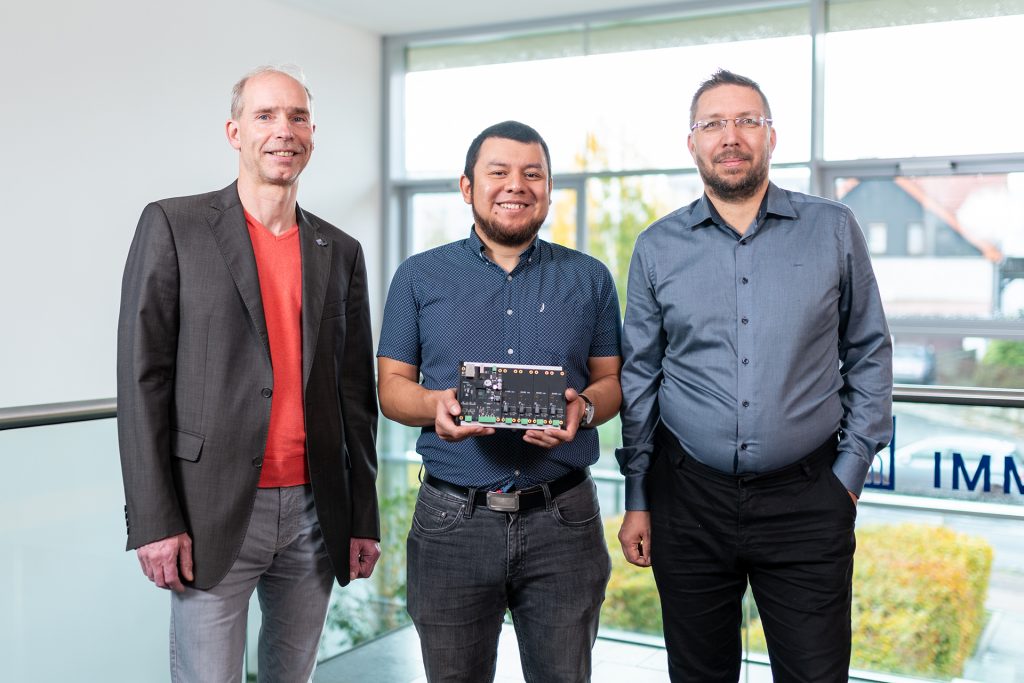
Dr.-Ing. Tino Hutschenreuther (Themenbereichsleiter System Design am IMMS), Jonathan Josue Gamez Rodriguez und Sebastian Uziel (Entwicklungsingenieure für eingebettete Hard- und Software am IMMS) mit der Sensorplattform „sUSe“ (v.l.)
Mit der Sensorplattform „sUSe“ stellt das IMMS Institut für Mikro elek tro – nik- und Mechatronik-Systeme gemeinnützige GmbH (IMMS GmbH) eine Lösung speziell für den Druckluftbereich vor. Ziel ist es, Undichtigkeiten in Druckluftsystemen und Wartungsstaus zu erkennen und zu beheben.
In Kooperation mit den Sensorik-Partnern SONOTEC GmbH (Ultraschallsensoren) und der Postberg+Co.GmbH (Volumenstromsensoren) wurde am IMMS mit sUSe eine automatisier- und skalierbare Lösung für diese Problemstellung entwickelt. Das sUSe-System kann in bestehenden Umgebungen nachgerüstet werden, um sie zu überwachen, die Energieeffizienz zu verbessern und damit letztlich auch CO2-Emissionen einzusparen.
Druckverlust führt zu Energieverlust
Druckluft dient in der Industrie zum Beispiel dazu, Maschinen anzutreiben, Bau- oder Kleinteile zu befördern oder Abluft-, Ventilations- und Trocknungssysteme zu unterhalten. In der Regel werden diese Druckluftsysteme mit einem elektrisch betriebenen Optimierung der Energieeffizienz und Wartung mittels Sensorik und Künstlicher Intelligenz Kompressor betrieben. Sobald also eine Undichtigkeit besteht, reduziert sich der Wirkungsgrad und gleichzeitig erhöht sich der Strombedarf, um die notwendige Leistung aufrechtzuerhalten. Es gilt daher einerseits, die Druckluft energieoptimal zu nutzen und andererseits, Leckagen zu eliminieren. Diese zu entdecken ist insbesondere dann problematisch, wenn die austretende Luft vom Menschen nicht wahrgenommen wird – etwa dann, wenn die Undichtigkeit zu klein ist. Treten mehrere solcher Fälle auf, kann sich das schnell summieren.
System integriert weltweit erstmalig Multisensorik und Datenfusion
Üblicherweise werden Lecks in Druckluftsystemen von extern beauftragten Service-Technikern mit unterschiedlichen Apparaturen identifiziert, analysiert und dokumentiert. Eine permanente Überwachung findet zumeist nicht statt. Die Daten lassen sich weder vernetzen noch in ERPSysteme übertragen. Die sUSe-Plattform bildet für all diese Varianten die Basis.
„Schon vor der Energiekrise hat die Industrie Leckagen in Druckluftleitungen bekämpft, da sie die meisten energetischen Verluste und damit auch unnötige Kosten verursachen. Mit Blick auf die aktuelle Preisentwicklung ist es für Unternehmen umso wichtiger, solche Undichtigkeiten zu finden, Verluste zu bewerten und Maßnahmen für die Instandhaltung einzuleiten.“
Hardwareseitig besteht das System aus der Plattform selbst und mehreren, über ein Druckluftsystem verteilten, vernetzten und fest installierbaren Ultraschall- und Volumenstrom-Sensoren. Die Volumenstromsensoren messen die Menge an durchfließender Druckluft an unterschiedlichen Stellen. Diese wird softwareseitig zu jener Menge in Beziehung gesetzt, die in das Druckluftsystem eingespeist wird. Die Ultraschallsensoren orten Leckagen akustisch und bewerten deren Verlust. Diese Daten werden dann fusioniert und digital verarbeitet.
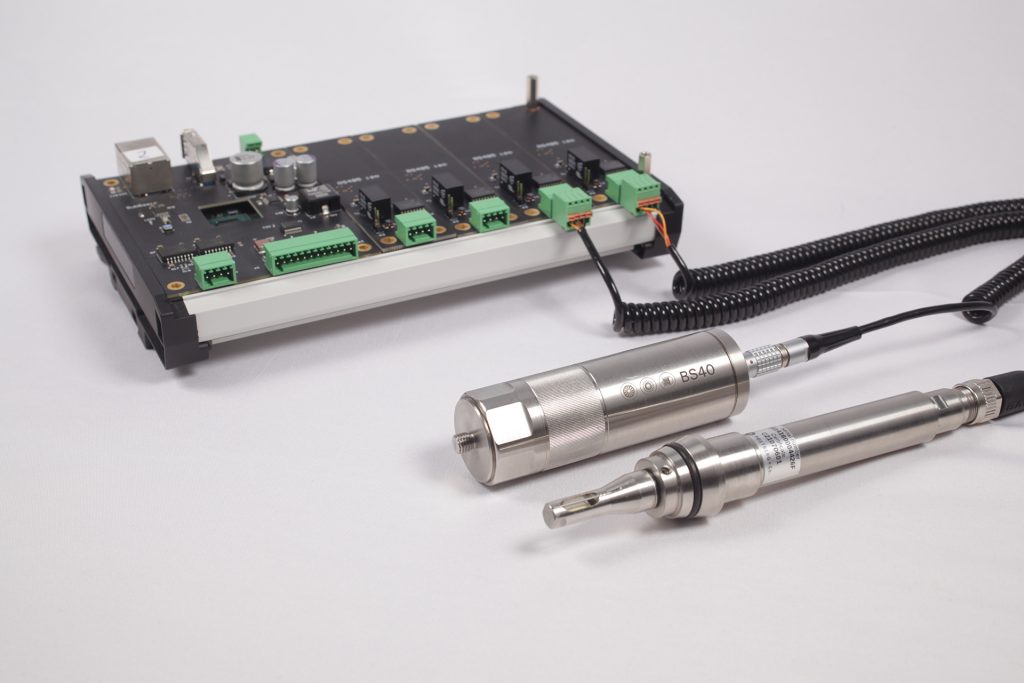
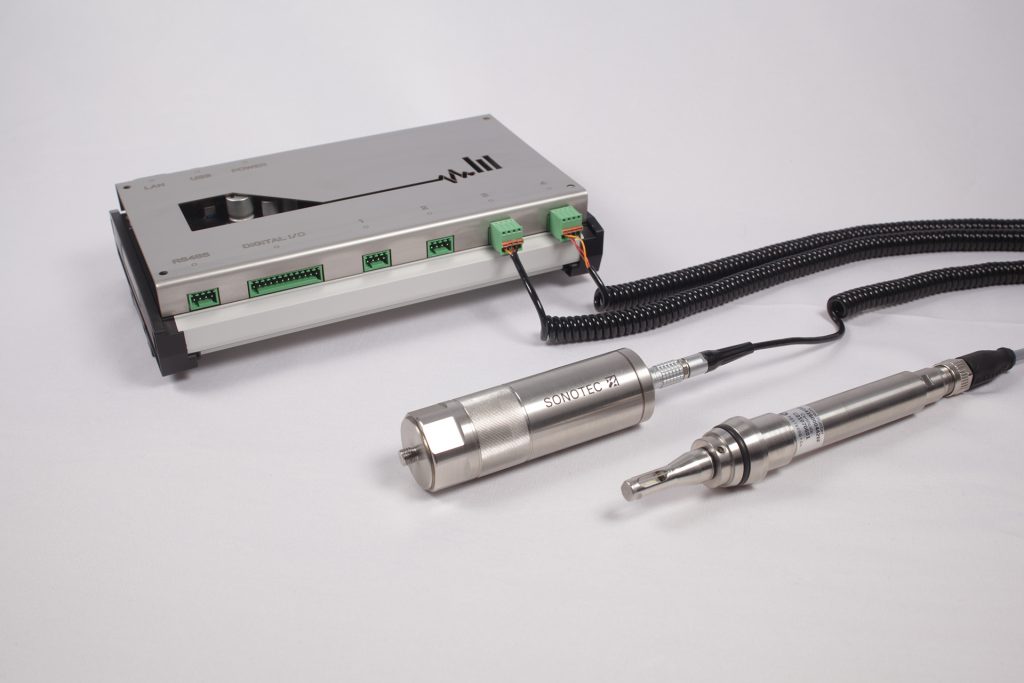
Das Herzstück der sUSe-Plattform mit angeschlossenen Sensoren
KI zur Zustandsüberwachung und vorausschauenden Wartung
Da Druckluft für viele Anwendungen an wechselnden Stellen in unterschiedlicher Menge zugeführt wird, müssen die sUSe-Plattform und alle zugehörigen Sensoren zeitsynchron arbeiten. Die Notwendigkeit der anschließenden prozessnahen Verarbeitung mit Algorithmen (Edge-KI) ergibt sich aus den hohen Datenraten der Sensoren. In den einzelnen Druckluftverteilsystemen erfolgt eine Verarbeitung unterschiedlicher Sensor-, Maschinen- und Anlagendaten mit dem Ziel, Anomalien zu detektieren und zu bewerten, Trends zu erkennen und Prognosen zum Wartungsbedarf unter Nutzung von KI- und speziell von Machine-Learning (ML)-Methoden zu erstellen. Erst die Datenauswertung und – im Idealfall – die visuelle Ergebnisdarstellung ermöglichen dies.
Maschinen und Anlagen sollten in ihrem Zustand überwacht werden, um Produktionsausfälle zu vermeiden. Beispielsweise können bei Druckluftkompressoren unterschiedliche Sensor- und Steuerungsdaten der jeweiligen Anlage im laufenden Prozess Aufschluss über Abweichungen, Fehler und absehbare Wartungsbedarfe an unterschiedlichsten Bauteilen des Kompressors geben, die sonst erst bei einem Ausfall bemerkt worden wären. Die Datenauswertung per Algorithmen ermöglicht einerseits eine Automatisierung, andererseits durch die Analyse von Mustern und Trends auch Vorhersagen.
Optionen für weitere (KI-) Anwendungen
Da die „sUSe“-Plattform über einen Steckplatz für KI-Beschleuniger verfügt, ist das System auch für das Online-Training von KI- bzw. ML-Modellen geeignet. Es kann daher direkt auf dem Edge-KI-System gelernt werden, weshalb es auch in der konkreten Einsatzumgebung im Unternehmen „dazulernen“ oder in Federated Learning-Architekturen zum Einsatz kommen kann. Im Gegensatz zu mobilen Diagnosegeräten kann ein fest installiertes System auf sUSe-Basis auch in Bereichen wie Roboterzellen oder automatischen Hochregallagern zum Einsatz kommen, wo Menschen keinen Zutritt haben oder dafür die Produktion unterbrochen werden müsste.
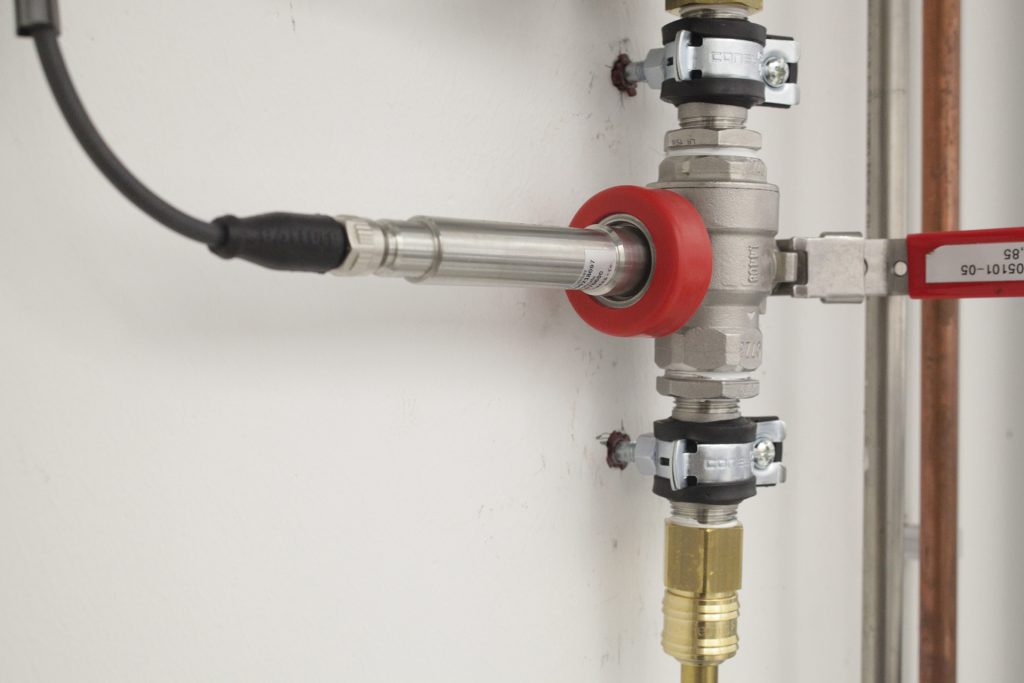
An ein Druckluftsystem angeschlossener Sensor
Über das Monitoring von Druckluftsystemen hinaus gibt es vielseitige Einsatzpotenziale in der vorausschauenden Instandhaltung (Predictive Maintenance), der Prozessüberwachung und der Qualitätssicherung. Die modulare Plattform-Architektur ist zudem so entwickelt, dass sich sehr spezifische Marktanfragen mit unterschiedlichen Sensorkombinationen effektiv bearbeiten lassen. (IMMS)
Das Projekt sUSe wurde unter dem Kennzeichen ZF4085709PO8 gefördert durch das Bundesministerium für Wirtschaft und Energie aufgrund eines Beschlusses des Deutschen Bundestages.