Lesedauer: 4 Minuten
Gastbeitrag: GFE – Gesellschaft für Fertigungstechnik und Entwicklung Schmalkalden e.V.
Qualitätskontrolle von Maßen und Oberflächen mittels KI
Kunststoffe, metallische Leichtbauwerkstoffe und auch technische Keramiken finden im Maschinenbau und in der Automobilbranche immer stärkere Anwendung. Die Sichtflächen sowie die Funktionsoberflächen müssen strengen qualitativen und optischen Anforderungen genügen.

Bildunterschrift: Lorem ipsum dolor sit amet, consetetur sadipscing elitr, sed diam nonumy eirmod tempor
Voraussetzung und Schwierigkeiten der Bauteilprüfung
Kleine Schwachstellen an Bauteilen sind mit dem bloßen Auge häufig nicht sichtbar, verringern jedoch maßgeblich die Qualität. Die Probleme intensivieren sich im Gebrauch des jeweiligen Bauteils mit der Zeit durch Temperaturunterschiede, Vibrationen und ähnliches und führen schlimmstenfalls zum vollständigen Defekt. Qualitätsmindernde Aspekte werden daher häufig mit hochauflösenden Kameras identifiziert. Problematisch allerdings ist, dass bisherige Verfahren die Prüfung großer Mengen von Bauteilen kaum ermöglichen. Notwendig hierfür ist einerseits die effiziente Prüfung der Kamera – zumeist mit vergrößernder Optik mit hoher Detailauflösung – und eine hochgradig akkurate Positionierung des zu prüfenden Bauteils unter der Kamera. Andererseits muss es intelligente Bildauswerte-Algorithmen geben, welche Abweichungen im jeweiligen Bauteil von Mustern vollständig funktionsfähiger Bauteile automatisch erkennen können.
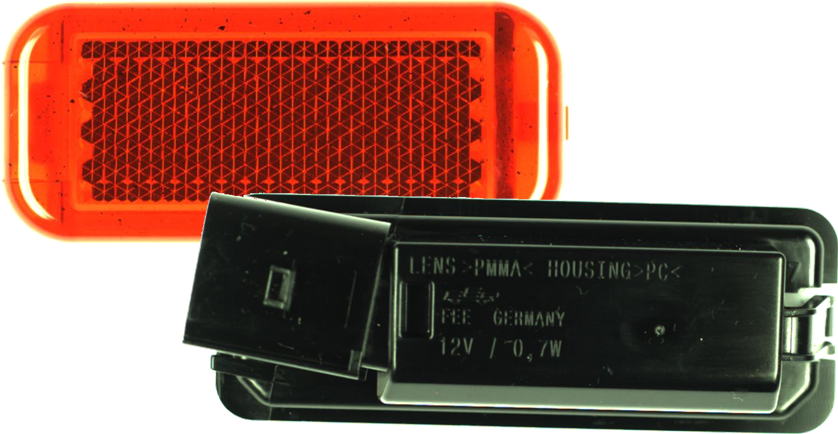
Zu prüfende Kunststoffteile aus dem Automobilsektor: Reflektor und LED-Gehäuse für Kennzeichenbeleuchtung
Die hohe Detailauflösung führt zu einem kleinen Sichtfeld und damit zur Notwendigkeit, große Flächen in mehreren Teilen aufzunehmen, welche später zu einem Gesamtdatensatz zusammengefasst werden. Aus diesem Gesamtbild sind geometrische Merkmale zu bestimmen und diese mit den Solldaten zu vergleichen. Der gesamte Ablauf muss zeitoptimiert ausgeführt werden, da das Ziel darin besteht, das System direkt in der Fertigungslinie (inline) einzusetzen und damit der Fertigungstakt die Anforderung an die Messzeit vorgibt. Insbesondere die Erzeugung von Datensätzen sowie der algorithmische Vergleich von geometrischen Ist-Daten mit den Sollwerten stellt aufgrund der hohen Datenmenge und der kurzen Taktzeit (mehrere Teile pro Sekunde) eine große Herausforderung dar.
Bildauswertung durch Deep Learning
Die wesentlichen Schritte zur Umsetzung der Qualitätssicherungsaufgabe bestanden in der Entwicklung einer angepassten Bilderfassung, eines Klassifikators basierend auf Deep- Learning-Verfahren (sogenannten Convolutional-Neural-Networks) sowie der Validierung des Gesamtsystems im Fertigungsumfeld. Im Ergebnis des Thüringer Verbundprojektes wurde erstmalig ein fertigungsintegrierbares und flexibles Verfahren vorgestellt, das sowohl eine objektive Sichtprüfung als auch eine präzise Maßhaltigkeitsprüfung an Kunststoffbauteilen in einem einzigen System realisiert.
Durch einen Knickarmroboter der Firma Kuka wird das Bauteil direkt aus der Spritzgießmaschine entnommen, unter eine speziell entwickelte Bildverarbeitungsstation gehalten, in mehreren Ansichten auf Fehler geprüft, vermessen und bei Fehlern direkt aussortiert. Für die schwarzen LED-Gehäuse sowie für die roten Reflektorbauteile konnte eine Erkennungsrate zwischen 95 und 100 Prozent in Abhängigkeit der zu erkennenden Defektklasse erreicht werden.
Praktische Anwendung
Das Prüfverfahren wurde prototypisch in das Fertigungsumfeld des Projektpartners Plasttechnik Hohleborn GmbH integriert und getestet. Die Defekterkennung und Vermessung ist ohne Verzögerungen im Produktionstakt möglich. Das der Entwicklung zugrundeliegende Forschungsprojekt wurde vom Freistaat Thüringen gefördert sowie durch Mittel der Europäischen Union im Rahmen des Europäischen Fonds für regionale Entwicklung (EFRE) kofinanziert. (GFE)
Das vom Freistaat Thüringen geförderte Vorhaben wurde durch Mittel der Europäischen Union im Rahmen des Europäischen Fonds für regionale Entwicklung (EFRE) kofinanziert.