Lesedauer: 3 Minuten
Vorhersagen können, wann ein Ausfall droht
Im Rahmen eines Produktions- und Bedatungsprozesses von Maschinen und Produkten fallen sehr viele Daten an,
die gezielt zur Verbesserung dieser Prozesse herangezogen werden können. Im vorliegenden Projekt wurde ein Prädiktionsmodell für Werkzeugmaschinen der DMG MORI Seebach GmbH erstellt, das auf Basis von Konfigurationsdaten den Ausfallzeitpunkt sowie die Ausfallursache einer Maschine vorhersagt. Mit Hilfe dieser Informationen kann die komplexe Konfiguration hinsichtlich Lebensdauer des Produkts optimiert werden.
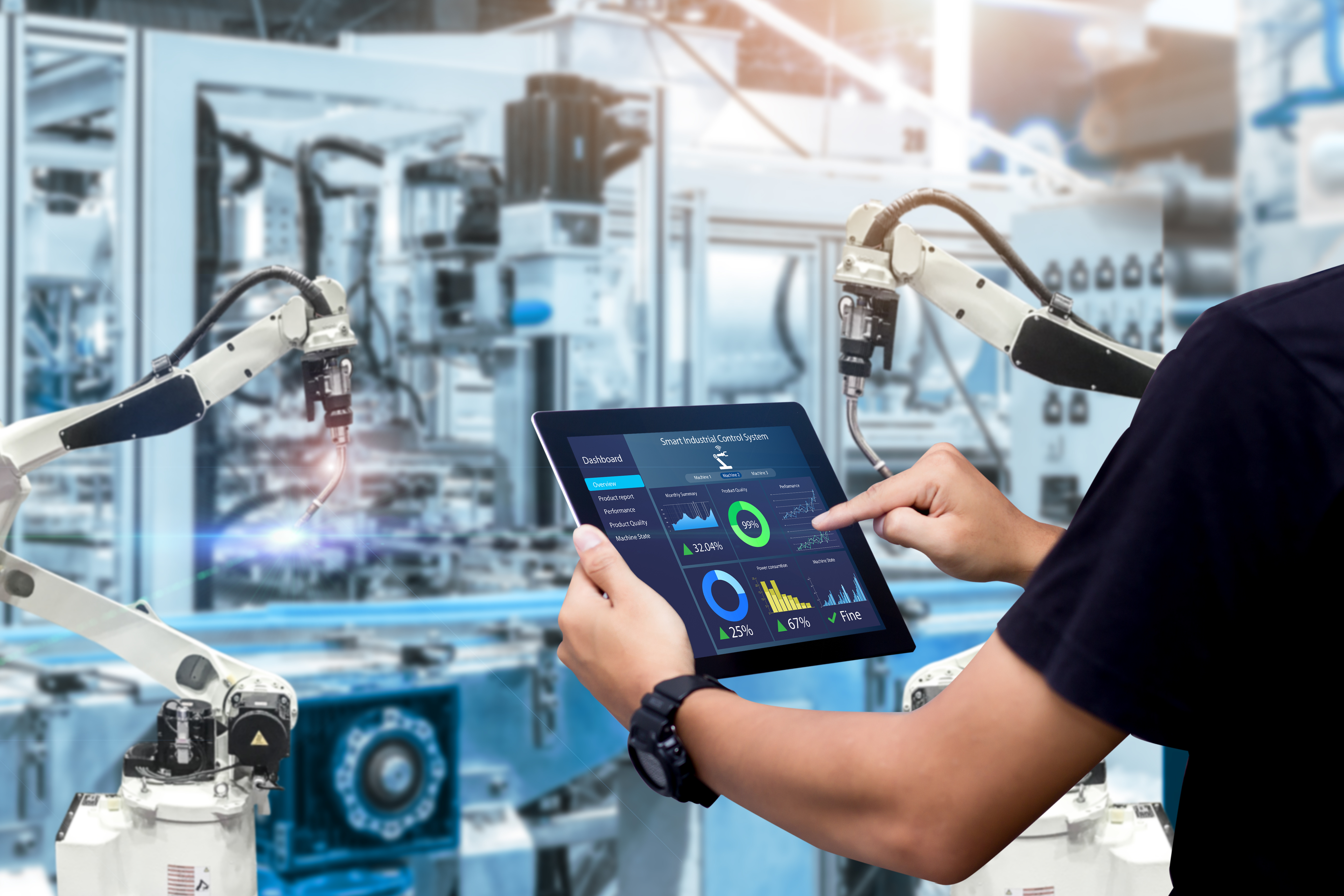
KI kann Daten auswerten, um Ausfälle vorherzusagen (Symbolbild) | Foto: panuwat – stock.adobe.com
Im ersten Schritt wurde das Modell mit Hilfe der Wiener‘schen Systemtheorie gebildet. Dieses systematische Vorgehen ist nötig, um möglichst abstrahiert die nötigen Daten zu identifizieren, die für die Aufgabe nötig sind (Top-Down-Ansatz). Außerdem orientiert sich das Projekt am CRISP-DM-Modell, das die Nutzung von Produktionsdaten zur Wertschöpfung in sechs Phasen beschreibt. Dabei steht die Ermittlung des Werts von Daten hinsichtlich der zu lösenden Aufgabe im Vordergrund. Hintergrund für dieses Vorgehen ist, dass häufig bis zum Schluss unklar ist, welche konkreten Daten in welcher Datenqualität nötig sind, um valide Aussagen mit Hilfe des Modells von Konfigurationen zu gewinnen. Auch die Signifikanz des Datenmodells ist damit definiert. Als Eingangsgrößen wurden Konfigurationsdaten definiert, als Ausgangsgröße die Ausfallursachen der Maschinen im Feld. Die Daten selbst wurden aus schwach strukturierten Konfigurations- sowie Prozessdaten sowie aus Erfahrungswissen aus unterschiedlichen Datenquellen gewonnen.
KI-Prädiktionsmodell für Feldausfallrisiken
Die schwach strukturierten Daten wurden mit Hilfe eines Matlab-Skripts in verarbeitbare Daten umgeformt, wobei das Skript selbst flexibel gegenüber neuen Daten programmiert wurde. Das ist notwendig, da im Laufe der Zeit neue Prozessdaten hinzukommen und/oder weitere Fehlerbilder sowie deren Zeitpunkte im Feld auftreten. Zur Realisierung wurden kategorische Vektoren (Hüllkurvenvektoren) angelegt, die für jede Konfigurations- sowie jede Fehlermöglichkeit ein binäres Feld vorsehen. Auch auf die Schwere des Fehlers wurde eingegangen, beispielsweise ein Ausfall der Maschine oder lediglich eine Fehlermeldung. Das Datenformat ist im Gegensatz zu numerischen Größen schnell verarbeitbar.
Mit Hilfe dieser Vorverarbeitung konnten nun vektoriell sowohl die 5.000 Ein- als auch Ausgangsdaten zusammengestellt werden und einem Algorithmus übergeben werden. Als lernendes System bieten sich künstliche neuronale Netze an, da die Zusammenhänge zwischen Modellein- sowie -ausgang nicht algorithmisch beschreibbar und zugleich hypernichtlinear sind. Auch bestehen mehr oder weniger starke Abhängigkeiten zwischen den Konfigurationsmöglichkeiten hinsichtlich der Ausfallursachen.
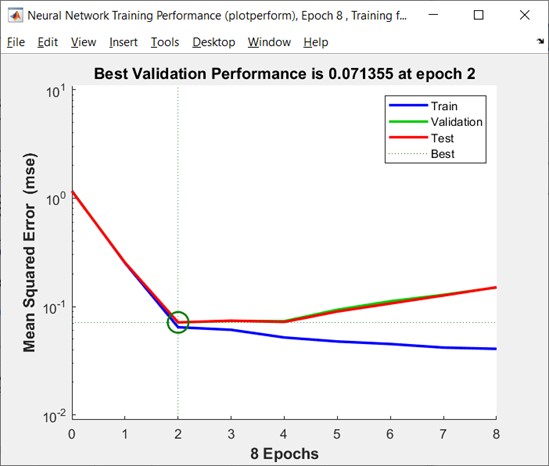
Fehlerberechnung durch Matlab über 8 Epochen hinweg | Grafik: Prof. Dr.-Ing. Christian Döbel
Vom Modell zur praktischen Nutzung
Zur Belehrung sowie Verifikation des künstlichen neuronalen Netzes wurden die vorhandenen Datensätze in Trainings- und Testdaten im Verhältnis 70/30 zufällig geteilt (innere Lernschleife). Die zufällige Aufteilung ist wichtig, um systematische Effekte zu unterdrücken. Danach erfolgte die Belehrung des Modells mit Hilfe der Funktionen der Neural Network-Bibliothek in Matlab. Neben beispielsweise Spyer (Python) konnte dabei die Bedatung vektoriell erfolgen und das entstandene Modell ist in andere Anwendungen exportfähig. Die Verifikation ergab einen Netzfehler für die Testdaten von 0.07, womit das Modell gültig ist. Dieser Vorgang wurde im Rahmen einer Kreuzvalidierung zehnmal wiederholt, um das Vorhersagemodell weiter zu verbessern (äußere Lernschleife). Eine Modellverifikation ist in diesem Schritt nicht vorgesehen, die die Komplexität der Vorhersage steuerbar machen würde.
Um das Modell zukünftig nutzen zu können, wird es im nächsten Schritt in unterschiedlichen Anwendungen (Desktopanwendungen und Apps) übertagen. Dabei ist es wichtig, kritische Konfigurationen der Werkzeugmaschine von vornherein zu vermeiden, indem sie durch unkritische möglichst von Anfang an ersetzt werden. Die Anwendungen sind einfach zu bedienen, um sie möglichst vielen Nutzern zugänglich zu machen.
Ein Reverse-Engineering des Modells kann nun spezielle Zusammenhänge zwischen kritischen Konfigurationen und bestimmten Fehlerbildern zutage fördern. Damit ist ein Rückschluss auch auf die Fertigungsmethoden und somit die Optimierung der Produktion möglich.
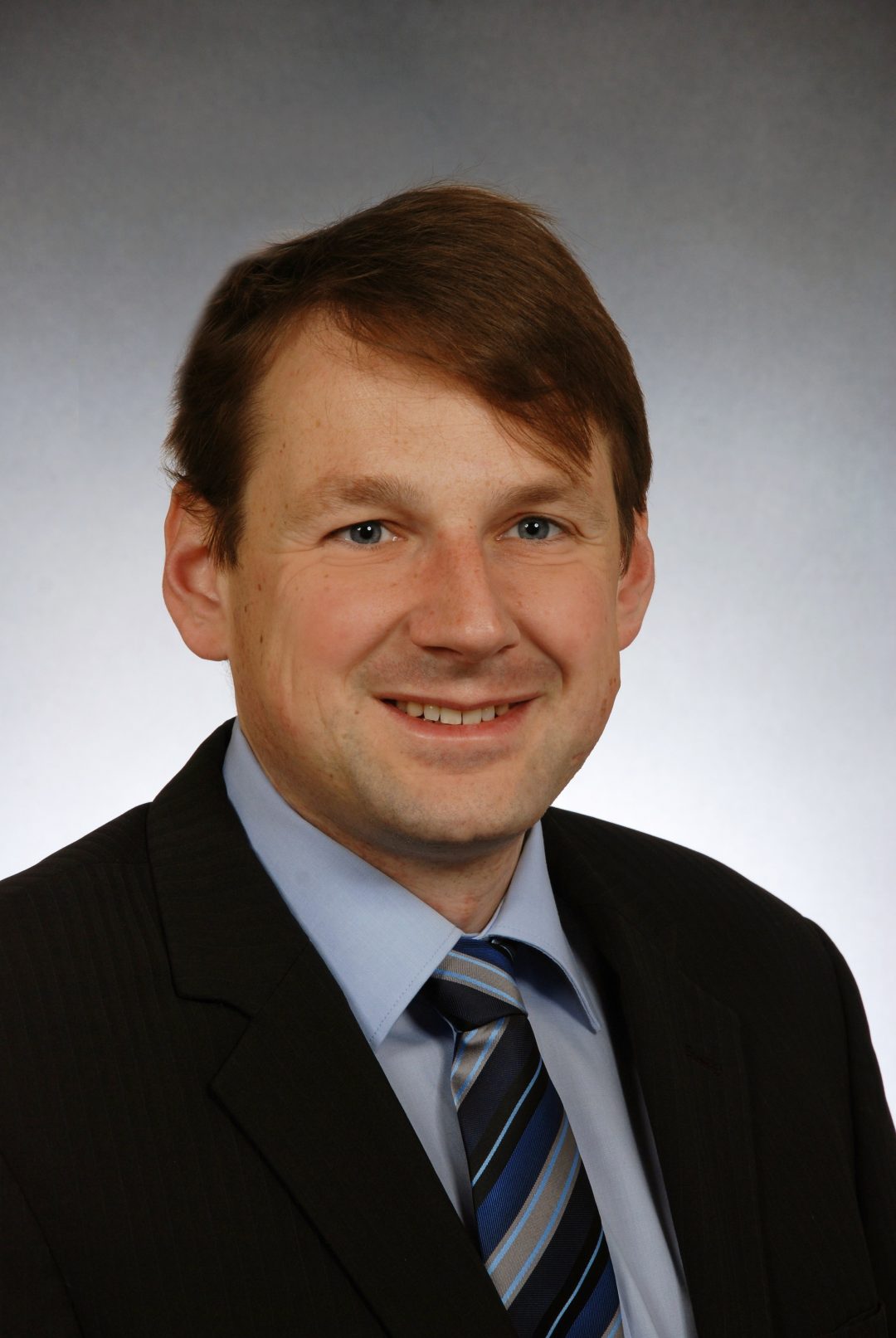
Prof. Dr.-Ing. Christian Döbel, Professor für Automatisierungs- und Regelungstechnik an der Dualen Hochschule Gera-Eisenach (DHGE) | Foto: Prof. Dr.-Ing. Christian Döbel